Metal Stamping: Advanced Techniques for Getting Precision and Performance
Metal Stamping: Advanced Techniques for Getting Precision and Performance
Blog Article
Checking Out the World of Metal Stamping: From Layout to Production
Within the world of production, steel stamping attracts attention as a specific and effective technique for shaping steel sheets into various forms with impressive consistency. From the initial layout stage where complex patterns take shape to the elaborate production processes, metal marking is a blend of virtuosity and design. Exploring this globe introduces a complicated interaction of imagination and technical mastery, offering a look right into a world where development meets workmanship.
Background of Steel Stamping
Metal stamping, an extensively used production procedure today, has a rich background that dates back to ancient times (Metal Stamping). The origins of steel stamping can be traced to old human beings such as the Egyptians, that utilized marking methods to embellish fashion jewelry and ornaments with intricate layouts. Over time, metal marking evolved, with human beings like the Greeks and Romans utilizing it for creating coins and attractive products

In the 20th century, metal stamping remained to advance with the integration of automation and computer mathematical control (CNC) technology. These developments additionally boosted the effectiveness and precision of steel marking procedures, making it a vital part of modern-day manufacturing throughout industries such as auto, aerospace, and electronic devices. Today, metal marking stays an essential manufacturing procedure, combining tradition with technology to satisfy the needs of a frequently developing market.
Layout Factors To Consider and Prototyping
When creating steel stamping tasks, thorough attention to design considerations and prototyping is necessary for ensuring ideal manufacturing end results. Layout factors to consider in steel stamping include product choice, part geometry, tooling style, and manufacturing usefulness. Selecting the best material is essential as it affects the part's efficiency, expense, and manufacturability. Part geometry affects the intricacy of the stamping process and the performance of the end product. Tooling layout plays a considerable function in the success of metal marking tasks, affecting part accuracy, device long life, and manufacturing performance.
Prototyping is an important phase in the steel marking process that permits engineers to evaluate the design, confirm manufacturability, and make essential adjustments before full-blown manufacturing. Prototyping helps recognize potential concerns early on, saving time and prices in the lengthy run. It likewise offers a chance to optimize the style for performance and high quality. By thoroughly thinking about design elements and making use of prototyping, manufacturers can streamline the steel marking process and accomplish high-grade, cost-effective production outcomes.
Tooling and Tools Basics
Considering the crucial function that tooling layout plays in the success of metal marking jobs, recognizing the vital tools and go to this web-site equipment needed is critical for attaining efficient production outcomes. Tooling is an essential aspect of metal stamping, as it straight influences the quality and consistency of the end products. Necessary devices consist of dies, punches, and fixtures, which are custom-made to form and create the metal into the preferred parts. Dies are the key tool utilized to cut and develop the steel, while punches help produce holes or details forms. Fixtures hold the steel in area during the marking process, guaranteeing accuracy and repeatability. Furthermore, tools such as stamping presses, feeders, and coil handling systems are critical for automating the marking procedure and raising efficiency. Buying high-grade tooling and devices not only enhances production effectiveness yet likewise causes greater accuracy, reduced waste, and total price financial savings in metal stamping operations.
Manufacturing Refine and Quality Control
Effectively handling the production process and carrying out robust quality control procedures are necessary for guaranteeing the success of metal stamping tasks. The production process in steel stamping includes a series of steps that must be thoroughly coordinated to accomplish optimal results. It begins with the prep work of resources, adhered to by the configuration of the marking devices and tooling. Operators then feed the materials into the press, where the stamping procedure occurs. additional info Throughout this procedure, it is crucial to monitor the assembly line for any type of issues that may influence the high quality of the stamped components.
Quality control in steel stamping is paramount to deliver products that meet the needed specs. By preserving rigorous top quality control requirements, makers can maintain their reputation for providing high-grade metal stamped click here for info items.
Applications and Market Insights
In the realm of metal stamping, the effective application of production processes and quality control measures straight influences the efficiency and reliability of numerous sector applications and supplies important insights into the sector's functional characteristics. In addition, steel stamping helps with the manufacturing of different household appliances, consisting of refrigerators, washing machines, and ovens, by offering cost-effective options for manufacturing long lasting and complex components. Comprehending the applications and industry understandings of steel marking is crucial for optimizing production processes and boosting product top quality across different sectors.
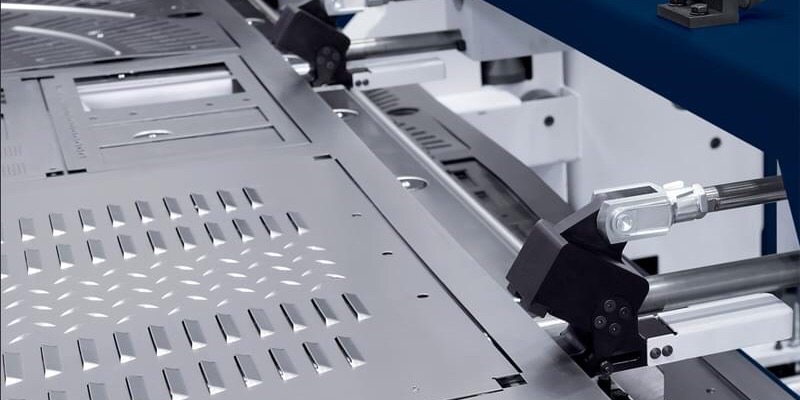
Verdict
Style factors to consider, prototyping, tooling, devices, production procedures, and quality control are vital elements of metal marking. With its widespread applications and sector understandings, metal marking proceeds to be a flexible and effective manufacturing procedure.
Report this page